In the fast-paced world of manufacturing, staying ahead often means embracing change. Soon, the only…
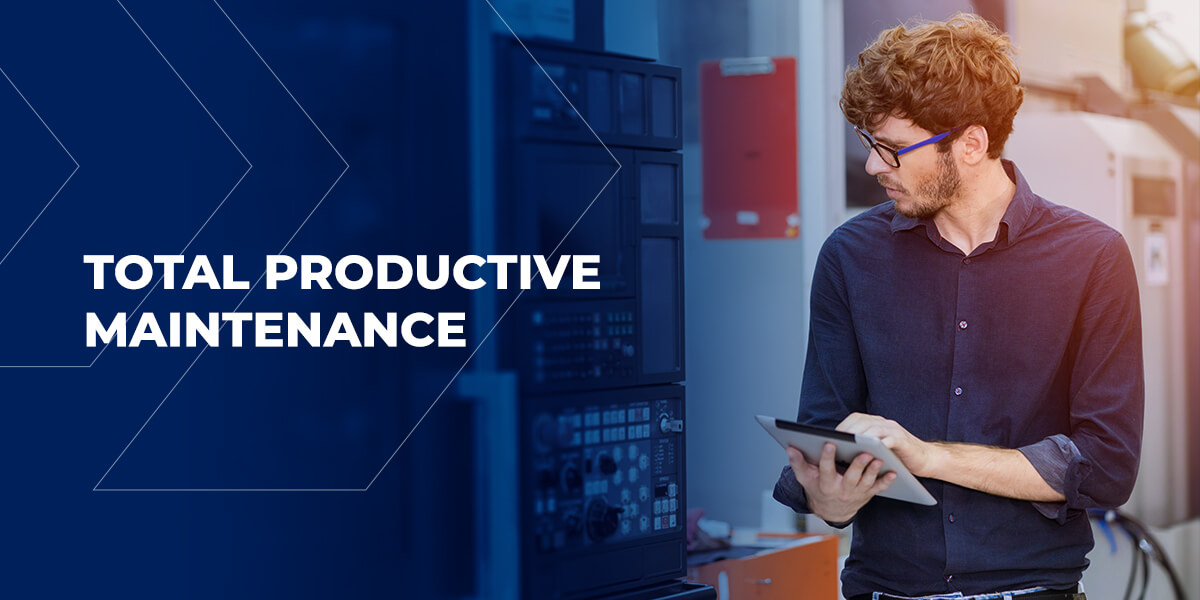
Table of Contents:
- What Is Total Productive Maintenance?
- The 8 Pillars of Total Productive Maintenance
- How Can TPM Be Used in Manufacturing?
- Total Productive Maintenance Implementation
Have you ever had a car or piece of equipment break down? And when you had someone look into fixing the equipment, several things needed to be repaired or replaced? If you’ve experienced something like this, you probably thought, “Wow, I wish I could’ve somehow prevented this from becoming as large of an issue as it did.” We have a solution for you.
Total productive maintenance (TPM) can prevent large breakdowns like those by helping you locate a small problem before it turns into a larger issue. MANTEC can help you maintain your machines and equipment to make sure everything runs as intended and find anything that could cause a problem later on. Discover more about this concept and how it can improve your business’s operations in this introduction to TPM.
What Is Total Productive Maintenance?
Total productive maintenance is a process in which equipment and machines are assessed. During this process, any issues that could cause failures or breakdowns are found before the problem escalates. Additionally, TPM ensures everything is working as efficiently as possible, which can help reduce your operating costs.
Why Is TPM Important?
You may believe that taking time out for maintenance checks and pausing your machines will slow down your operations and create too much downtime. However, there are some important reasons why businesses perform total productive maintenance:
- It allows for a safer working environment: Safety is the most essential aspect of doing TPM. If a machine breaks down or shorts out, it could cause a fire or another dangerous situation. An emergency like this creates issues for your employees and workplace, including endangering the lives of those working near the machine.
- It can decrease unplanned maintenance time: If you’re working on a deadline to get something done, it’s frustrating to stop work to wait on something to be fixed. With TPM, you’ll know ahead of time if there are any mechanical issues that could cause a problem, which lowers the risks of unplanned downtime.
- It helps achieve “perfect production”: Of course, nothing is ever perfect, but TPM can get you as close to perfect as possible. TPM reduces downtime and failures, which means machines run as efficiently as possible to produce product and profit.
With these benefits of TPM, you can understand why it’s important for your machines and equipment to receive regular and comprehensive maintenance.
The 8 Pillars of Total Productive Maintenance
Before delving into TPM, it is important to remember the main goals of the process, which are no accidents, no breakdowns and no defects. To have the most success with using total productive maintenance, always keep these goals in mind.
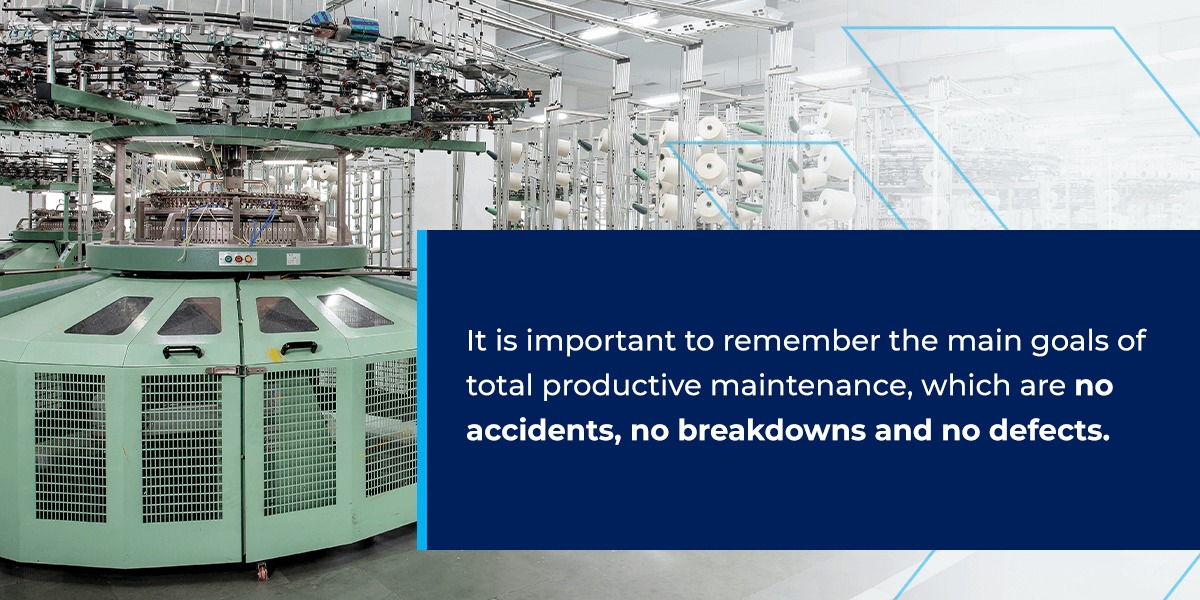
The pillars of TPM are also referred to as the basic principles. If you want your total productive maintenance strategy to be as effective and helpful as possible, you’ll want to follow these key elements:
- Autonomous maintenance: Each employee is responsible for contributing to the upkeep of the machines and equipment they use. Every mechanical component in your facility should be cared for by machine operators and maintenance staff.
- Process and machine improvement: Every business’s goal is to improve while keeping costs and losses down. Every machine operator should watch for anything that seems out of the ordinary. They should be willing to reflect with the other machine operators to find new avenues that could lead to improvements, whether with the machines’ performance or their own duties.
- Preventative or planned maintenance: This type of upkeep involves the regular periodic maintenance done on equipment to ensure everything is in working order and ready to perform with no issues.
- Early management of new equipment: When new equipment is acquired, it can be beneficial to use knowledge of past experiences when operating these machines. Let’s say a duplicate machine was purchased because your company is expanding and needs to produce more materials. Because you already have one of these machines, you’ll know what issues it may have or which parts will go out of service and when. You can prepare for these things in advance to reduce any downtime for that machine.
- Process quality management: One of the main goals of TPM is to have zero defects. To uphold process quality management, analyze how machine operators manage and interact with equipment. Make sure they are avoiding any actions that could be contributing to breakdowns or defects.
- Administrative work: This pillar ensures everyone is involved in machine upkeep — even the administrative team. Whether admins are physically involved or only provide research, they should also have a hand in TPM. For TPM to work as effectively as possible, the entire staff must make an effort, not just those working with the machines.
- Training and education: Continuous training and education should be mandatory for all machine operators, especially because technologies are constantly changing. Incorporating regular training and providing educational materials is the best way to make sure machine operators are properly trained, which can reduce breakdowns, defects and downtime.
- Safety and sustained success: Safety in the work environment should always be a priority. Following good maintenance protocols can improve your workplace’s safety and health, thereby increasing and sustaining your company’s success.
By following these total productive maintenance pillars, you can achieve your main goals and maximize production and profits with your equipment and machines.
How Can TPM Be Used in Manufacturing?
If your equipment isn’t working at its best ability, your enterprise isn’t manufacturing or producing at its best, which can hurt your business. The implementation of a TPM program can help your business get back on top. Here’s how to start:
- Pick your target: Which equipment seems to have the most problems? Which equipment would be easiest to improve? Where does your manufacturing process need some help? Identify these key areas so you can receive specific results.
- Restore the equipment using the autonomy pillar: Ensuring everyone on the team has a defined responsibility and detailed strategy for maintaining machinery will help you locate any issues.
- Track the overall equipment effectiveness (OEE): Your business’s OEE is the amount of planned production time that includes truly productive work. Tracking this helps you better see areas of improvement.
- Cut down losses: Use your findings so far to locate and decrease the losses you’ve been previously experiencing.
- Implement TPM: To keep up the momentum of step four, implement the eight pillars of TPM into your company’s operations to ensure minor issues are caught before escalation. Integrating TPM will also help you maximize production.
Choose MANTEC for Total Productive Maintenance Implementation
MANTEC is a nonprofit manufacturing service provider that strives to help smaller manufacturing businesses remain competitive and efficient in the industry. As your service provider, we can supply you with anything you may need to meet your goals and improve profit within your company. We will also help you integrate a total productive maintenance strategy for your equipment if you’re ready to make the switch.
To speak with a specialty advisor, fill out our contact form or call us at (717) 843-5054. We’d love to help you!